【行业】锂电设备竞争激烈优质企业脱颖而出(36页)
锂电池的生产工艺较为复杂,主要生产工艺流程涵盖前、中、后三个阶段:前段工序的目的在于将原材料加工成为极片,经过、涂布、辊压、分切、制片、模切等工序,其中核心工序为涂布;中段目的在于将极片加工成为未激活电芯,需要经过卷绕或叠片、入壳焊接、注液和封口等工序,其中卷绕、叠片是中段的核心工序;后段目的在于激活电芯使之成为成品电池包通过 PACK 集成系统最终进入电池厂,包括清洗、干燥储存、检测、喷码、化成分容等工序,最终通过自动化智能物流系统进入下游生产线,其中化成、分容是后段的核心工序。按照工艺流程所对应锂电设备也可分为前段设备、中段设备和后段设备,分别被运用于这三个生产阶段。设备价值量方面,前、中、后段工序设备在整个设备投资中所占比重约为 4:3:3。
锂电池的后处理是在电芯完成之后对电芯进行激活、检测和品质的判定,具体包括电芯的化成、分容、分选等工作,经过后处理之后,电芯才能达到可使用的状态。根据生产工艺的不同,电芯充放电次数也不完全相同,但至少进行两次,第一次是化成,第二次是分容。“化成”从原理上来说就是激活电芯(使得电池中的活性物质第一次充电转成正常电化学作用,并使得并使电极主要是负极表面生成有效钝化膜或 SEI 膜),使电芯具有存储电的能力,类似于硬盘的格式化。“分容”即“分析容量”,又叫“分容测试”,就是将化成好的电芯按照设计标准进行充放电,以测量电芯的电容量。分容需要对电芯进行一次完整的充电及放电,计算并记录充放电全过程的电压、电流、恒流充电时间及容量、恒压充电时间及容量、放电时间及容量,充电能量、放电能量、温度等物理量。
充放电设备是整个后处理系统中最重要的设备之一,也是后处理系统中使用量最多的设备。充放电机的最小工作单位是“通道”,在充放电机实际使用中,一个“单元”由一定数量的通道组合而成,工作时为若干个电芯同时进行充电或放电。若干个单元(BOX)组合在一起,就构成了一台充放电设备。充放电设备在对电芯进行充放电的同时,也会记录下充放电的相关数据和曲线表,如电流、电压、时间等等,作为计算电芯电容量及评价电芯是否合格、如何分类的依据。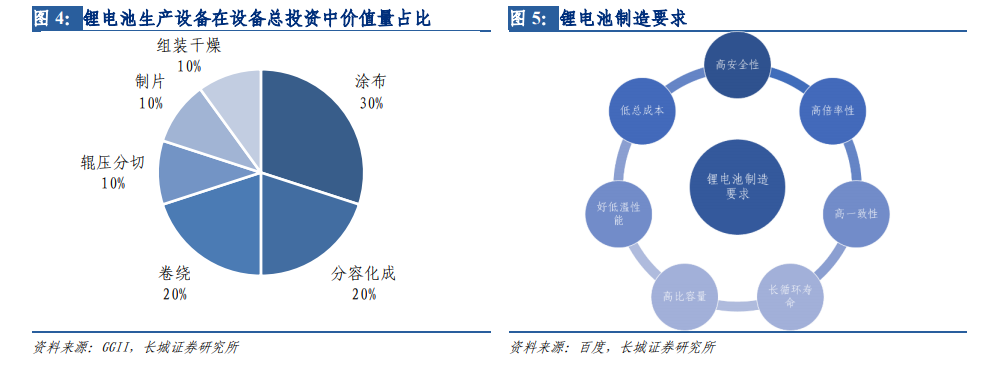
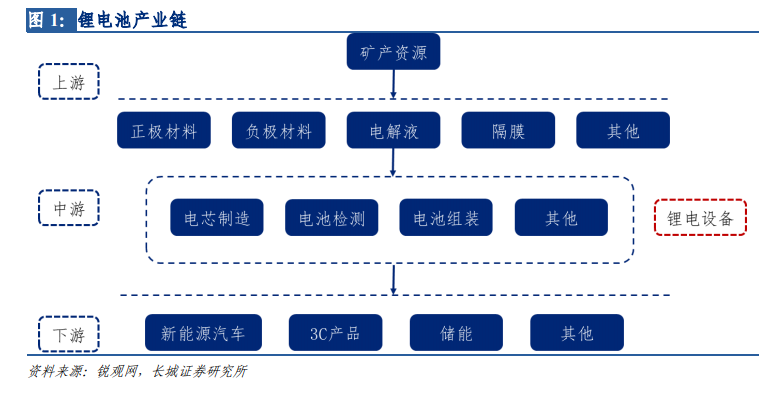
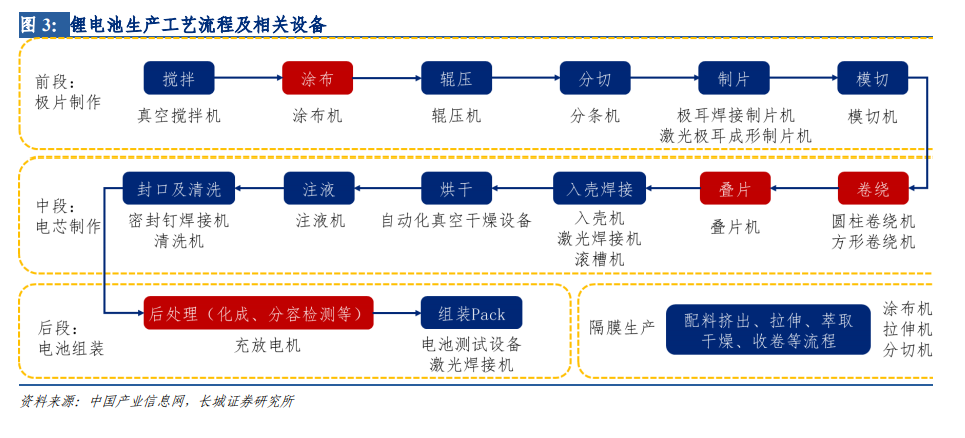
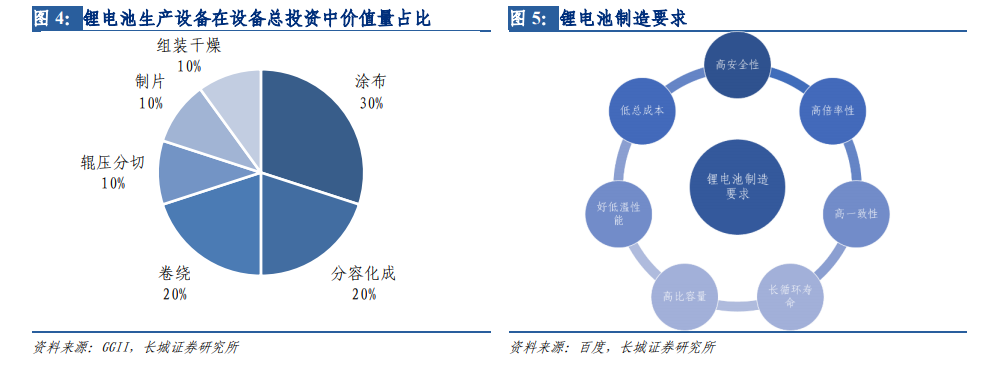