【行业】新能源汽车行业-结构创新频出(65页)
驱动因素1:续航里程提升趋势下,轻量化需求强劲。在不改变电池系统总能量的情况下,电池系统质量降低能够有效提高其续航里程,电动汽车质量减10%,能提高续驶里程5.5%。电池系统重量在新能源汽车总重量中占有较大的比重。较传统燃油汽车而言,电动汽车核心的三电系统(电池、电机、电控)和智能化设备,使得电动车相比同类车型电动乘用车重量增加10%-30%,电动商用车重量增加10%-15%,其中电池Pack整包占整车整备质量的18%~30%【《从三方面入手推动新能源汽车轻量化》(原诚寅,2020)】。根据《节能与新能源汽车技术路线图2.0》,到2035年,燃油乘用车整车轻量化系数降低25%,纯电动乘用车整车轻量化系数降低35%,相比于燃油车,新能源汽车轻量化需求更强。
驱动因素1:续航里程提升趋势下,动力电池创新加速。解决动力电池“续航里程”焦虑的主要途径有三种:一是新的正负极材料、电解液等关键材料的创新;二是新的电池体系的建立;三是新的电池工艺、工艺、结构、技术创新,都着力于提升电池容量。相比于材料体系创新,结构创新能在更短时间内帮助大幅提升电池(包)的能量密度。为了提升电动车的续航里程,通过改进底盘空间内的空间利用率,放入更多动力电池以增加实际带电量,是电池结构创新的重要手段之一。 在维持整车质量稳定的前提下,电池数量的提升势必导致结构件的减少和动力电池电芯集成方式的革新,对于动力电池胶粘剂需求也将进一步提升。
轻量化路径:材料轻量化、结构集成化齐头并进。材料迭代+结构优化,轻量化结构件。以特斯拉Model3为例,电池Pack各主要部件中,质量最大的是电芯本体(62.8%),其次为Pack下箱体(6.2%)、模组壳体及支架(12.3%)和BMS等部件集成系统(11.1%)等。从这些部件出发,通过材料替换和结构设计优化,对电池进行轻量化开发。对于电芯模组轻量化设计,可通过改进电芯排布优化电芯间距;利用能量密度高的材料作为电芯正负极;使用密度较低的灌封胶解决热传导问题;减少模组对于电池pack和底盘轻量化设计,除了电池Pack采用铝合金等轻质的材料之外,还可通过CTB、CTC等技术,将电池和车身进一步集成化。减少模组壳体及其他附件质量的数量从而大幅降低电池质量;小模组-大模组-CTP-CTC/CTB,动力电池集成方式创新精简模组壳体和非必要部件质量。 在轻量化趋势下,结构件和焊接减少,从而增加了胶粘剂的使用量。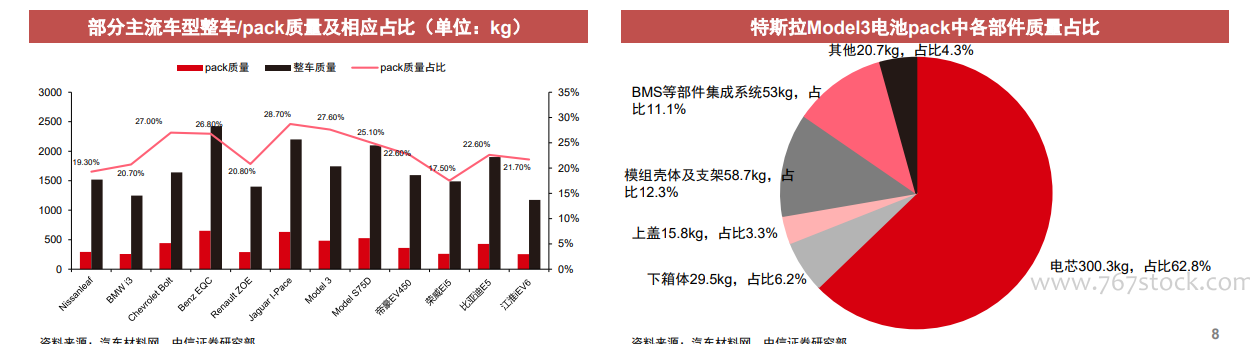
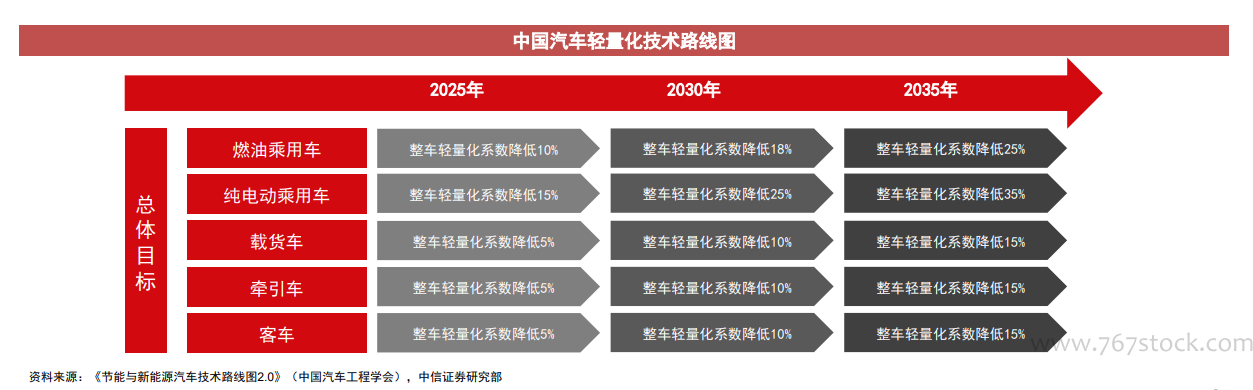
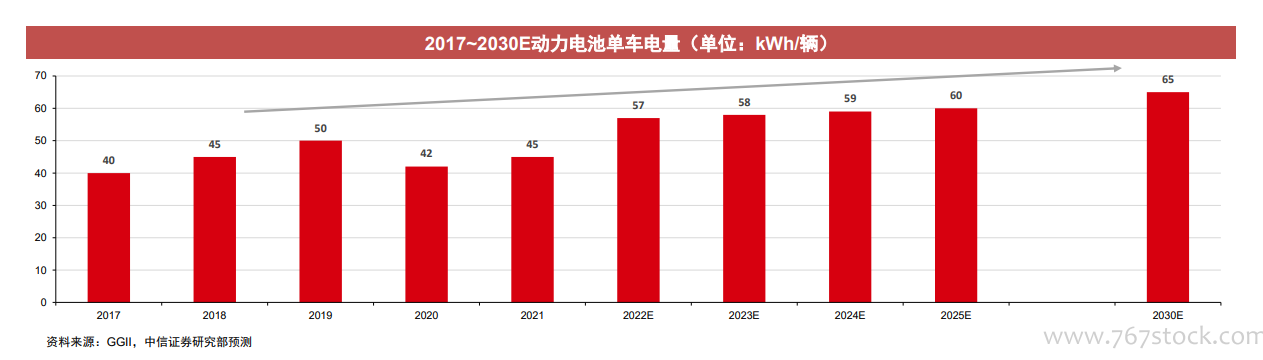
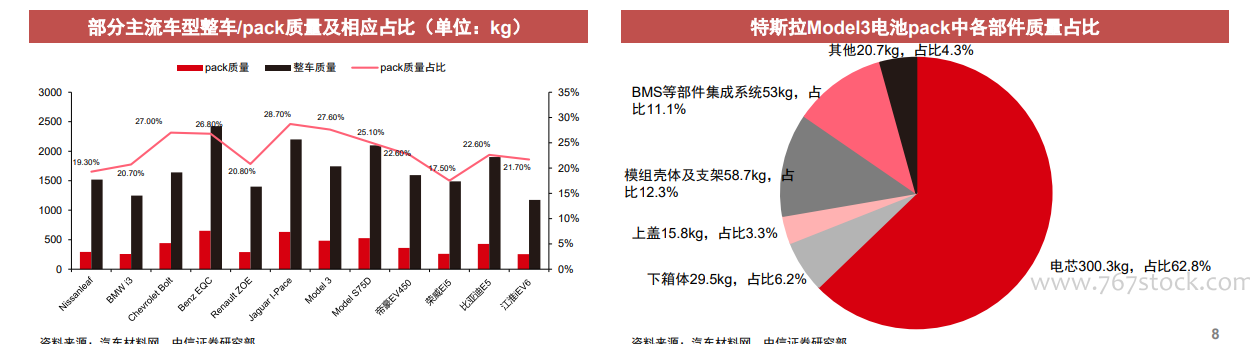