【行业】储氢瓶用碳纤维赛道-氢风已来大有可为(24页)
国内储氢瓶市场预计将逐渐向 III 型 70Mpa 和 IV 型 70MPa 过渡。2020 年 7 月 21日,涉及车载高压供氢系统的两项国标修改后正式实施,均将原范围中的工作压力不超过 35MPa 修改为 70MPa。2021 年 3 月 9 日《燃料电池电动汽车加氢口》(GB/T26779-2021)最新国家标准正式发布,新国标增加了 70MPa 加氢口尺寸及耐臭氧老化、耐盐雾腐蚀、耐温度循环和兼容性测试等多项技术条目,制约 70MPa 储氢瓶发展的政策条件已经消除。并且,从储运效率、轻量化、成本等角度出发,IV 型瓶相较于 III 型瓶具备显著优势,未来将成为车载供氢系统的主流规格,1)III 型瓶重容比在 0.98 左右,IV 型瓶重容比在 0.74 左右;2)III 型瓶储氢密度为 3.9%,IV 型瓶储氢密度可以达到 5.5%;3)IV 型瓶单瓶气体容积可达到 375 升,可降低整个系统复杂性。当前我国还处于 35MPa的 III 型瓶规模化应用和 70MPa 的 III 型瓶示范应用阶段,IV 型瓶尚未得到大规模推广应用,背后原因一是由于我国氢能及燃料电池产业发展起步较晚,技术水平落后于海外,二是配套基础设施建设缓慢,目前国内加氢站规模较小且以 35MPa 为主,三是政策及技术标准体系尚未建立健全。后续来看,各方面限制因素将持续改善。伴随着燃料电池汽车的大规模推广,为满足进一步长续驶里程的需求,未来车载储氢瓶规格有望由 III 型35MPa 向 III 型 70MPa 或 IV 型 70MPa 过渡,逐步与国际技术水平接轨。
III 型瓶内胆多为铝合金,目前国内使用的主流成型工艺为铝管强旋,所谓强旋就是将短厚的毛坯铝筒体套在旋压机的模具上并将其固定,当筒体随机床主轴转动时,用旋轮或赶棒从端头开始挤压筒体坯料,使坯料逐点连续发生塑性变形,变形的结果是毛坯壁厚减薄,内径基本保持不变,而轴向延伸,最终形成符合壁厚及直径尺寸要求的圆筒。该种工艺相对简单,但生产效率较低,尤其是用来加工大容积内胆时成型效率低下。目前国内头部企业有在研究其他更高效的成型方法比如拉深成型,该种工艺优势在于生产效率高、产品一致性好、圆周壁厚均匀、纵向垂直度偏差小,缺陷在于可能影响产品的疲劳寿命,且设备成本较高;此外也有企业尝试将两种工艺结合使用,比如先拉成筒状体再进行强旋。
纤维缠绕成型也是储氢瓶制备的技术难点之一,目前使用的工艺包括湿法缠绕、干法缠绕和半干法缠绕。1)湿法缠绕是指将碳纤维丝束在特定浸胶装置中浸渍处理后,再在张力控制下直接缠绕到芯模上。由于纤维离开浸渍装置后易于将树脂带出,后道工序中存在树脂滴漏的现象,所以称为湿法缠绕。湿法缠绕工艺生产成本较低,是目前高压储氢瓶最常用的加工工艺,国内企业基本都采用湿法。但湿法成型下树脂损耗较高,树脂与碳纤维比例难以控制,产品质量及稳定性相对较差。2)干法缠绕是以经过预浸胶处理的预浸带为原料,在缠绕机上经加热软化至粘流态后缠绕到芯模上。由于预浸带中纤维和树脂含量比例控制较好,产品质量可以精确控制,且树脂不会随处滴,整体生产环境整洁;另外,干法缠绕生产效率高,缠绕设备的速度可以达到 100-200m/min。目前国外正在逐步向干法缠绕工艺过渡,国内未势能源等极个别企业也在研究和尝试干法。此种工艺的缺点在于成本较高,主要系预浸料及干法缠绕设备购置费用较高。3)干湿法缠绕结合了干法和湿法的优点,在浸胶碳纤维缠绕到芯模之前通过烘干设备将浸胶碳纤维纱线中的溶剂除去,提高制品质量。与干法缠绕相比省却了预浸胶工序和设备,与湿法相比只是增加了一套烘干设备,却可以大幅降低制品中的气泡含量以及孔隙。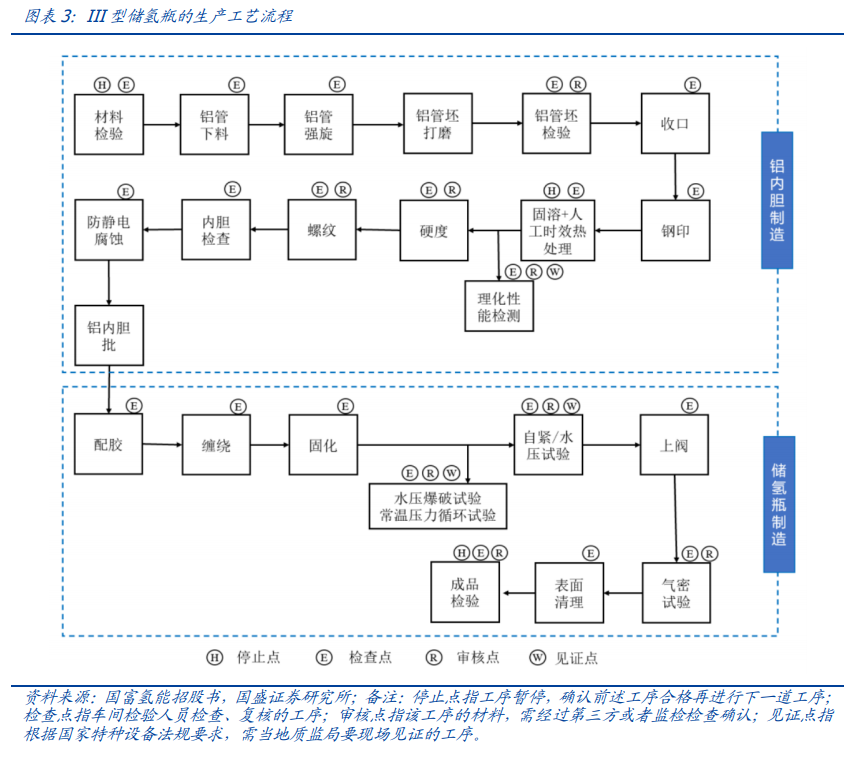

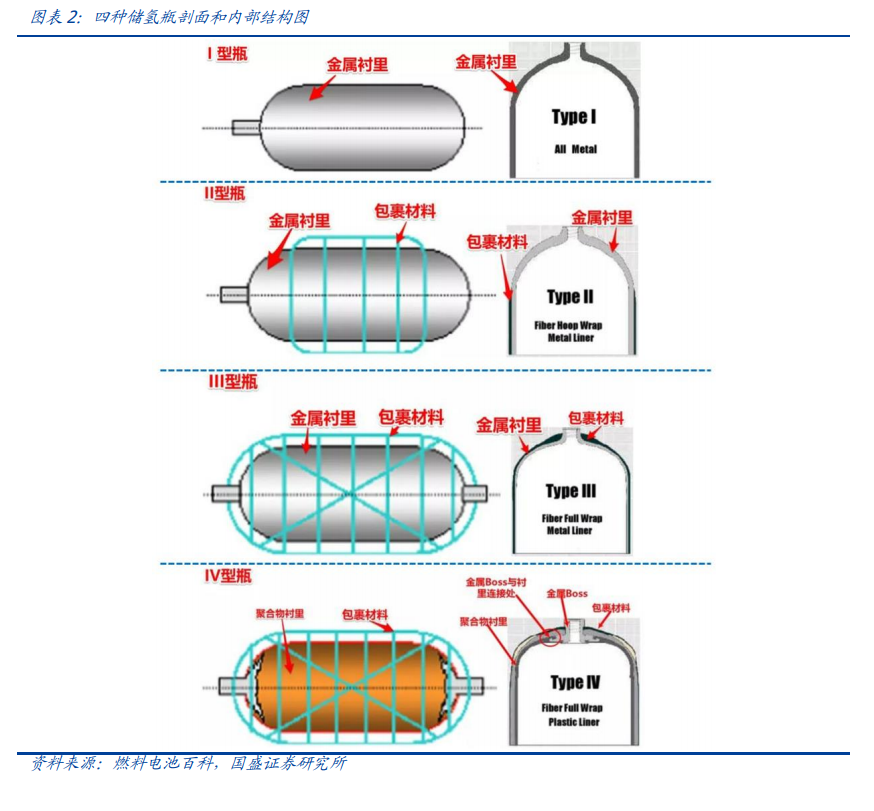
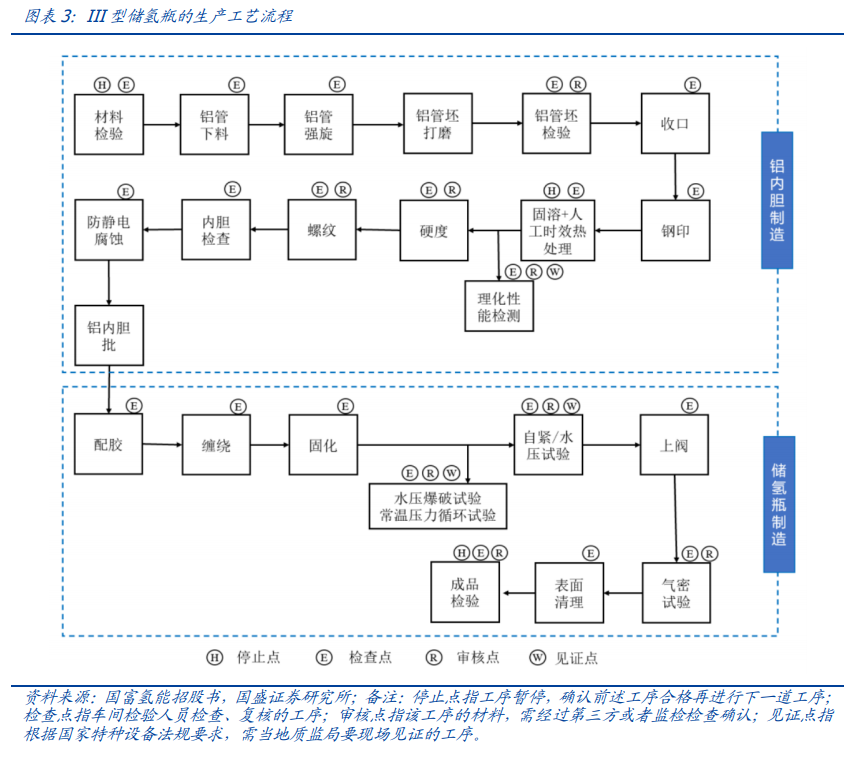